NEMA 34 Stepper motor is a hybrid stepper motor that has the best attributes of the variable reluctance stepper motor as well as a permanent magnet stepper motor. This is a heavy motor and draws a high current of up to 5A. The motor takes 200 steps during a single revolution with a step angle of 1.8 degrees and a 3.4×3.4 inch faceplate. It is a 2-phase motor with a step accuracy of ±5%. It is controlled by microcontroller units indirectly through appropriate motor drivers.
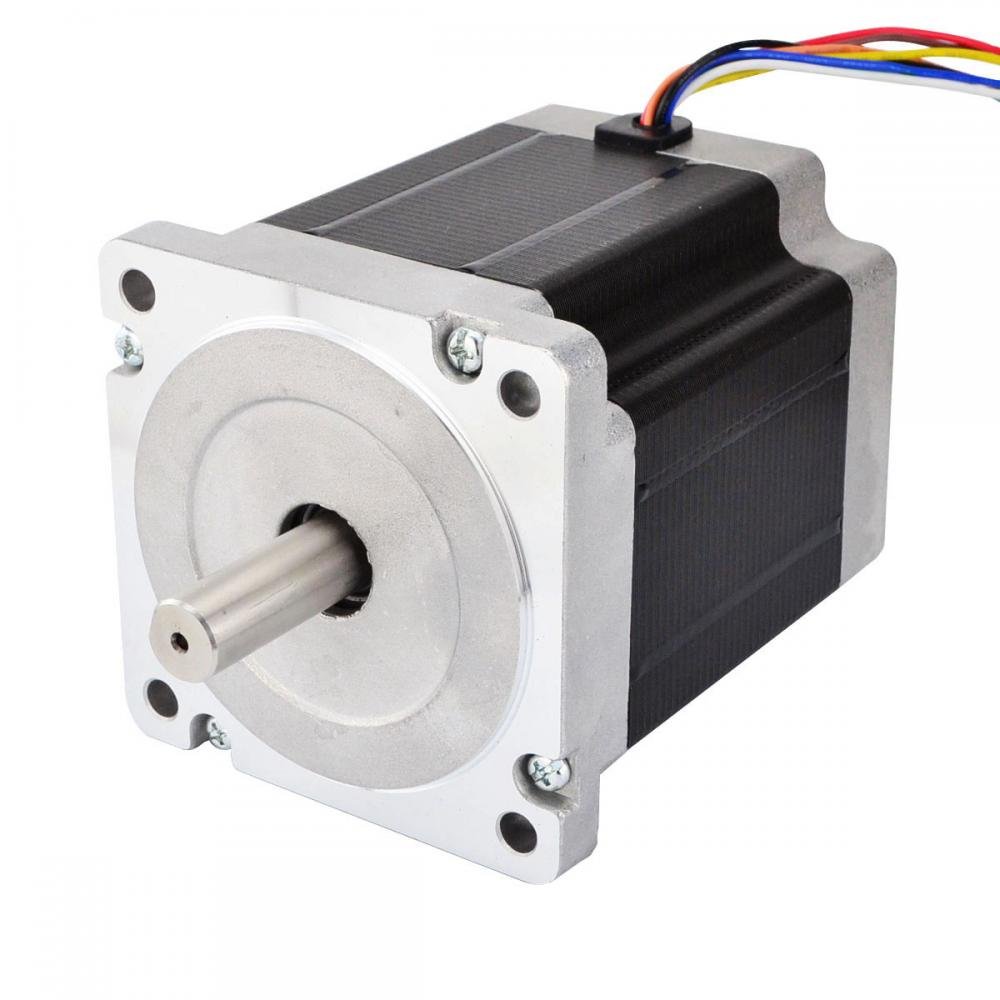
NEMA 34 Stepper motors are available in different versions depending on torque holding capacity, current ratings, rotor inertia, and physical dimensions. They are used in computer numerical control machines, 3D prototyping, robotic projects, and in different industrial equipment.
NEMA 34 Pinout
The following diagram shows the pinout of the NEMA 34 Stepper motor:
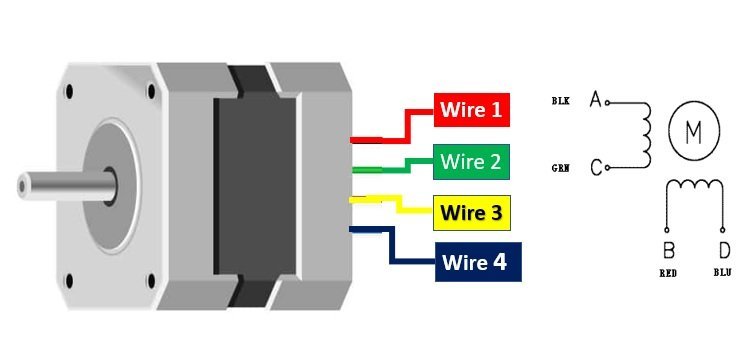
Wire Details
Let us discuss the pinout of the NEMA 34 Stepper motor. The wire configuration detail in tabular is mentioned below:
Wire Color | Function |
---|---|
RED | Motor Coil1 connection |
GREEN | Motor Coil1 connection |
BLUE | Motor Coil2 connection |
YELLOW | Motor Coil2 connection |
Working of NEMA 34 Stepper motor
The stepper motor as the name suggests works on the stepping principle. It means that the motor completes its rotation in the form of steps. The motor receives pulses from the controller to move steps and complete a rotation. One pulse received equals one step. With each step, it covers a specific step angle that provides control over the position of the motor. Typically the number of steps is 200 and the step angle is 1.8 degrees.

The frequency of the pulses is directly proportional to the speed of the motor. To increase the speed of rotation, one must increase the frequencies of the pulses.
NEMA 34 Specifications
- Current Ratings: 4A – 5A
- Unipolar Holding Torque Capacity: 2.2 – 6.4 Nm Min
- Bipolar Holding Torque Capacity: 3.1 – 9.0 Nm Min
- Step Angle: 1.8 degrees
- Steps per Revolution: 200 steps
- Step Accuracy: ±5%
- Resistance Accuracy: ±10%
- Inductance Accuracy: ±20%
- Maximum Temperature Rise: 80°C
- Ambient Temperature: -20°C to 50°C
- Minimum Insulation Resistance @ 500V: 100Mohms
- Dielectric Strength @ 3mA: 820 VAC
- Radial Play @ 450g: 0.02mm
- End Play @ 450g: 0.08mm
- Radial Force: 220 N
- Axial Force: 60 N
NEMA 34 Stepper motor has five different versions based on current ratings, holding torque capacity, phase inductance e.t.c. The datasheet is provided to see further technicalities as per requirement.
Interfacing NEMA 34 Stepper driver with Arduino UNO
The section deals with the interfacing of the NEMA 34 Stepper motor.
As the NEMA 34 stepper motors are heavy duty so they cannot be connected directly to the microcontroller unit. It should be interfaced with a proper stepper motor driver module for functioning. These are compatible with STP-048, STP-140, CW-2450,CW-230 e.t.c that can sustain high current. The enable, pulse, and dir pins of the respective stepper motor driver are connected to the Arduino UNO pins. The enable pin serves to empower the driver module. The pulse pin is the step pin that controls the micro-stepping of the motor by pulse reception from the Arduino. Similarly, dir configures the rotation of the motor either clockwise or anticlockwise depending on its state.
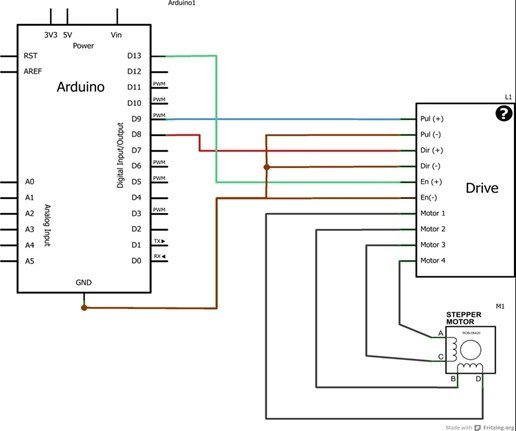
The outputs motor1, motor2, motor3, and motor 4 are connected to the coils of NEMA 34 stepper motors. The controller sends the pulses to the driver and it transmits it to the motor. The motor takes steps and completes the rotations in the direction told by the state of the dir pin and can work according to the demand.
Applications
- Welding tools
- CNC machines
- Medical systems
- 3D applications
- Robotics
2D Diagram
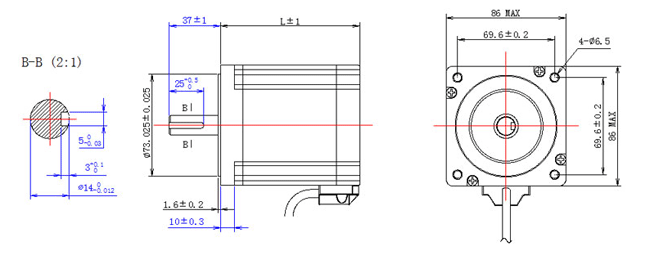
Datasheet
Related Articles:
- Stepper Motor Interfacing with TM4C123 Tiva Launchpad
- NEMA 23 Stepper Motor Pinout, features and example with Arduino
- STEPPER MOTOR INTERFACING WITH 8051 MICROCONTROLLER
- 28BYJ-48 5 volt Stepper Motor Guide
- PC Controlled Stepper Motor System Using PIC Microcontroller
- STEPPER MOTOR INTERFACING WITH PIC16F877A MICROCONTROLLER
- DC Motor Speed and Direction Control with TM4C123 and L298N Motor Driver